Success Story: Pik Rite, Inc. Implements Strategies Learned Through IMC’s CI Programs with Positive Impact on Production
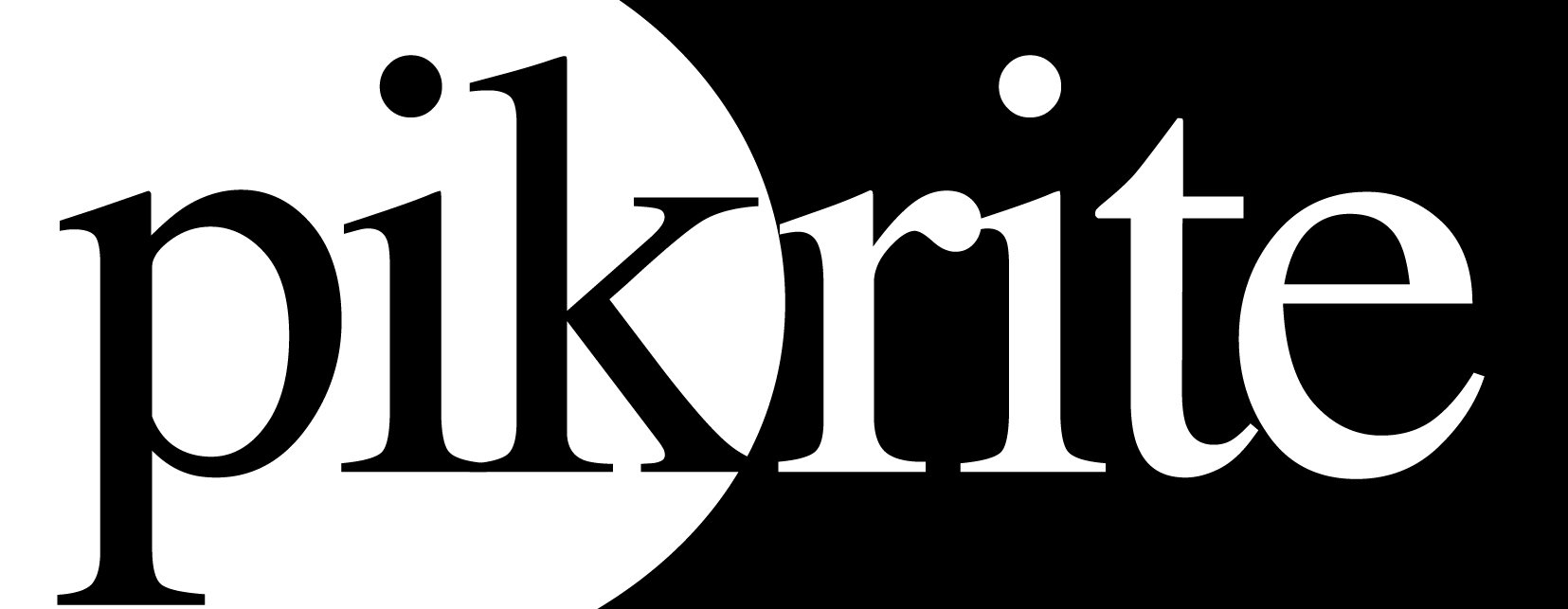
Pik Rite was founded by Elvin Stoltzfus and Joe Yoder with a focus on creating a mechanical method for picking tomatoes. Their first machine was built in 1983, and by 1986, Pik Rite had manufactured three harvesters and incorporated the company.
From its initial tomato harvester, Pik Rite has diversified its product line to include equipment for harvesting cucumbers, peppers, gourds, zucchini, squash, pumpkins, and carrots. Additionally, Pik Rite produces vine diverters, commercial waste handling vacuum tanks, water hauling trailers, truck mounted dump bodies, manure spreaders, and municipal leaf collection units. Pik Rite also has a dedicated contract manufacturing line.
Pik Rite has steadily grown since the 1990s, expanding its market coverage, sales, and technological innovations both domestically and internationally. Based in Central Pennsylvania, the company now employs nearly 100 people across two facilities in Lewisburg, PA.
With continuous growth in business and varied industrial and agricultural markets, Pik Rite sought to increase production capacity and capabilities while maintaining their high-quality standards and design flexibility.
Pik Rite faced several critical challenges in their production process that hindered efficiency, employees, and ultimately customer satisfaction. The main bottleneck was cumbersome production flow due to fragmented processes, which led to frequent delays and increased operational costs. Material handling issues further complicated these inefficiencies, as the lack of streamlined systems resulted in frequent delays and product mismanagement. Employees reported dissatisfaction stemming from repetitive, unnecessary tasks, impacting overall morale and productivity. This ultimately resulted in strained relationships with clients.
Pik Rite has a long-established relationship with the Innovative Manufacturers’ Center (IMC) and IMC is a contributor to Pik Rite’s continuous improvement journey. Pik Rite selected several personnel to attend the IMC’s Lean Level 1 and 2 certification programs to seek potential strategies to address its current challenges in production as well as to build on its mission to give everyone “the opportunity to grow personally while engaging in an atmosphere of unity, respect, and integrity.”
Through both the training program and post training assessments, Pik Rite implemented strategies learned from the IMC certification programs that included but were not limited to:
- Streamlined receiving and storage methods in the material warehouse to eliminate waste and improve material flow.
- Implemented a small parts handling system in the fabrication shop to reclaim lost floorspace, eliminate wasted motion, and improve overall flow and efficiency.
- Relocated materials in the fabrication shop for easier access for fabricators.
- Created multiple travel lanes throughout the entire facility to provide direct access from the fabrication shop to the production floor.
- Implemented a smart organization and carting system for Harvester fabricated parts.
- Started a safety hazard removal initiative in the fabrication shop.
These changes led to increased flow in the fabrication shop and production area, reducing the time employees spend searching for materials. Raw materials now flow into the storage areas seamlessly and can be retrieved safely and quickly by the operators.
Fabrication has become approximately 15% more time efficient while utilizing full sheets of raw material. Production now tracks and utilizes 100% of their remnant material, up from approximately 25%. Overall throughput has increased by 8-10% with these changes and has even spiked to 20% in unique scenarios. Since implementing a safety hazard removal initiative in the fabrication shop, Pik Rite has had zero incidents, improving from 1-2 reported incidents per month, previously.
“The IMC and its staff have played an integral part in the success of Pik Rite’s Continuous Improvement culture as well as directly influencing more efficient production and operations. The proof is in our results – our workplace is safer, our employees are happier, and we’re getting more quality work delivered to our customers, faster.”
Caleb Thomas, Product Line Manager