Introduction to Lean Manufacturing with Simulation
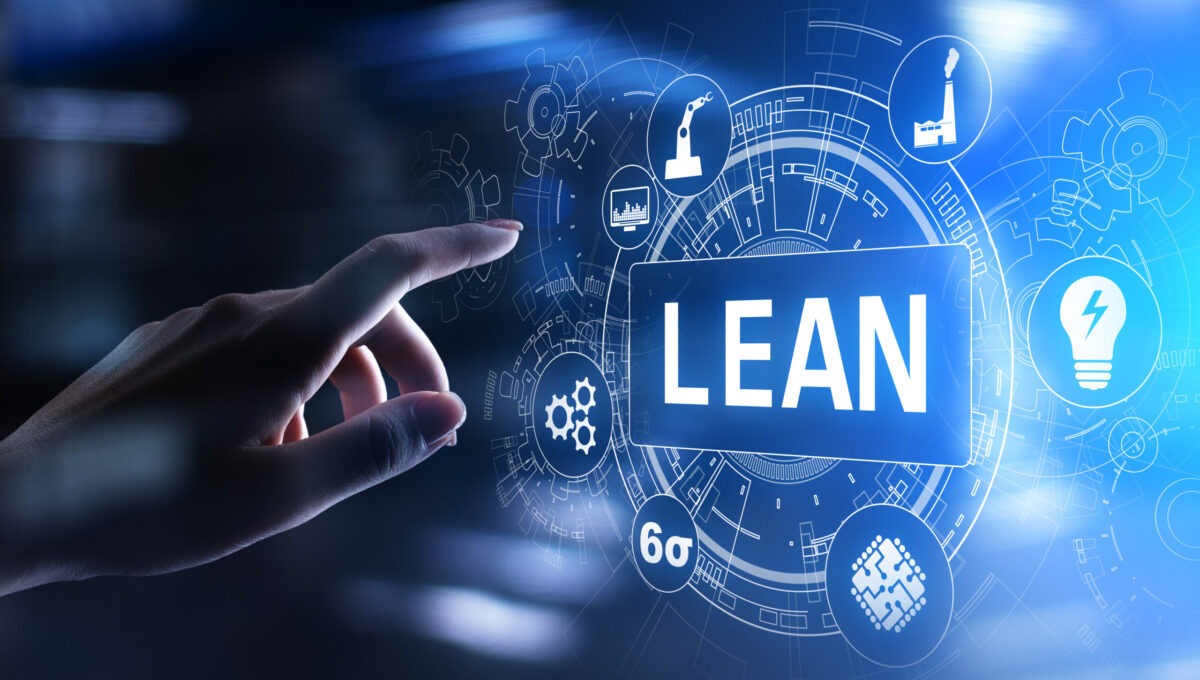
Introduction to Lean Manufacturing with Simulation
(6-hour, in-person, Altoona, PA)
This program starts in:
In today’s fast-paced, competitive environment, improving efficiency and eliminating waste is crucial for long-term success. This 6-hour Lean Manufacturing course is designed to equip participants with a fundamental understanding of Lean principles that drive real, measurable improvement in company operations. Participants will dive into essential Lean tools and methods, such as Value Stream Mapping, Workflow Analysis, Pull Production, 5S Workplace Organization, Visual Management, and more. You’ll explore how each technique solves specific problems and contributes to smoother workflows, reduced waste, and improved bottom lines. With hands-on exercises in a simulated environment, attendees will not only learn the theory behind these tools but also apply them in practice. By the end of the course, participants will understand how to assess improvement opportunities, choose the right techniques for your organization, and implement strategies that ensure success.
Register now for only $389 per person!
Learning Objectives:
- Understand and apply the 5 core principles of Lean thinking to drive continuous improvement.
- Differentiate between value-added activities, non-value-added activities.
- Recognize the eight types of waste and develop strategies to reduce them for optimal efficiency.
- Use value stream mapping to identify bottlenecks and improve flow across processes.
- Gain insights into key Lean methods and learn how each technique addresses specific operational challenges.
- Apply Lean tools in a hands-on, simulated environment to experience real-world impact.
Course Outline:
- Introduction to Lean Manufacturing
- Understand the fundamentals of Lean principles and their impact on operational efficiency.
- Simulation – Round 1
- Apply traditional manufacturing practices in a simulated environment to observe current processes.
- Round 1 Debrief
- Analyze results from Round 1 and discuss key learnings and opportunities for improvement.
- Overview of Traditional Manufacturing
- Examine traditional manufacturing practices and understand how Lean differs and improves upon them.
- Introduction to Process Improvement & Systems Thinking
- Explore the importance of viewing processes holistically and understanding interdependencies for continuous improvement.
- Key Lean Tools: Value Streams, Standard Work, Flow, and Visual Management
- Learn to identify value streams, implement standard work, and apply visual management techniques for better organization and flow.
- Simulation – Round 2
- Apply new Lean concepts in the simulation to create measurable improvements.
- Round 2 Debrief
- Review the results of Round 2 and identify areas for further refinement.
- Advanced Lean Techniques: Pull Scheduling, Batch Size Reduction, Setup Reduction, TPM, and Cellular Flow
- Delve into more advanced Lean methods designed to optimize production scheduling, reduce waste, and improve machine efficiency.
- Simulation – Round 3
- Implement the advanced techniques in the final simulation to test improvements and optimize flow.
- Round 3 Debrief
- Reflect on the outcomes of Round 3 and discuss final adjustments for continuous improvement.
- Strategies for Successful Lean Implementation
- Learn how to effectively implement Lean practices in your organization to ensure long-term success.
- Course Conclusion
- Recap key takeaways and next steps for applying Lean manufacturing techniques in the real world.
Register now for only $389 per person!
Who Should Attend:
Operators, Technicians, Engineers, Supervisors, and Managers
Why Attend:
Elevate your manufacturing operations by attending our “Introduction to Lean Manufacturing with Simulation” workshop. Here’s why this opportunity is essential for your business:
- Master Lean Principles: Gain a comprehensive understanding of Lean methodologies to drive continuous improvement and operational excellence.
- Identify and Eliminate Waste: Learn to pinpoint inefficiencies within your processes and implement strategies to reduce waste, leading to cost savings and enhanced productivity.
- Enhance Workflow Efficiency: Discover how to streamline workflows, minimize bottlenecks, and improve process flow to boost overall efficiency.
- Hands-On Experience: Engage in practical simulations that allow you to apply Lean tools and techniques in a controlled environment, ensuring you’re ready to implement them in your operations.
- Boost Customer Satisfaction: Implement Lean strategies to improve product quality and delivery times, resulting in higher customer satisfaction and loyalty.
Don’t miss this chance to transform your manufacturing processes and achieve sustainable success. Join us and take the first step toward a Leaner, more efficient future.
Instructor:
Max Krug, Owner and Change Management Champion at Future State Engineering, has 30 years of experience in operations, and his range of expertise and experience includes manufacturing operations, distribution, and project management environments. His expertise is assisting organizations achieve Operational Excellence by utilizing Theory of Constraints, Lean Management, and Six Sigma methods. He works with companies to develop corporate strategy and provides hands-on implementation support of the tactics required to achieve Operational Excellence utilizing these techniques. Max holds several certifications in Theory of Constraints, Lean, and Six Sigma in addition to a B.S. in Industrial Engineering from Alfred University and an MBA from St. Bonaventure University.