Lean Manufacturing Practitioner Certification
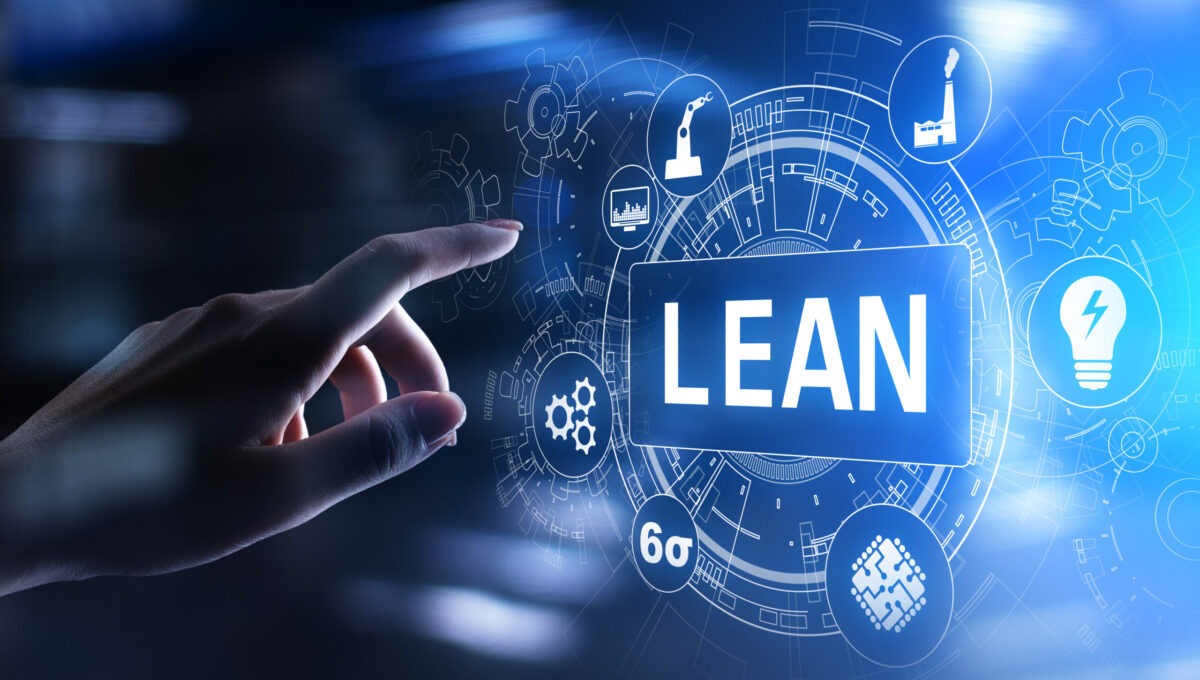
Lean Manufacturing Practitioner Certification
(5-day, in-person, Williamsport, PA)
This program starts in:
Imagine being able to pinpoint areas within your operations where resources are being underutilized, or unnecessary steps are slowing down production. Through practical, hands-on workshops, you’ll learn how to systematically improve these processes, leading to reduced expenses and improved profitability. The Lean Manufacturing Practitioner Certification is your gateway to transforming your manufacturing processes and driving significant improvements in your business. By participating in this certification program, you will gain essential skills to identify and eliminate wasteful practices, ultimately saving costs and increasing efficiency.
Register now for only $1,795 per person!
Learning Objectives:
This course equips you with the ability to:
- Foster a culture of continuous improvement within your organization
- Understand and apply lean tools such as value stream mapping, workplace organization, change management, teaming and kaizen methodology
- Learn collaborative problem-solving techniques
- Enhance overall productivity and employee engagement
- Turn data into actionable information in order to quantify problems and prioritize countermeasures
Lean Manufacturing Practitioner Certification Flyer
Program Outline:
Day 1 – May 12, 2025
- Introduction to Lean
- Batch Simulation
- Lean Assessment – Value Stream Analysis
- Project Selection – Lean Team vs. Kaizen
Day 2 – May 13, 2025
- 5S – Sort, Scrub, Shine, Standardize, Sustain
- Managing Constraints
- Load Leveling
- Data Collection
- Single Minute Exchange of Die
Day 3 – May 14, 2025
- Process Flow Design
- Principles of Ergonomics
- Standard Work
- Supermarket Strategy
- Pulling Flow – Kanban
Day 4 – May 15, 2025
- Total Productive Maintenance (TPM)
- Supplier Integration
- Visual Management
- Reporting Results
- Financial Tracking
Day 5 – May 16, 2025
- Creating Implementation Plan
- Communicating Lean
- Continuous Learning of Lean Principles
- Discussion and Q&A
Schedule:
This 5-day (34 hours) program is May 12 thru May 16, 2025. Monday thru Thursday 8:00 a.m. – 4:00 p.m., Friday 8:00 a.m. – 12:00 p.m.
Register now for only $1,795 per person!
Why should you attend?
- Gain knowledge for using A3 methodologies, improving team communication, reducing collaboration challenges
- Learn the value stream mapping (VSM) process to help you identify waste, reduce lead times, standardize workflows keeping costs low and efficiencies high
- Boost team productivity by making every minute count, streamlining processes to reduce waste and create a safe workplace that fosters innovation
- Improve communication at all levels of your organization, changing hurdles and obstacles into opportunities for change and transition
- Create an individualized roadmap linked to your company objectives that ends frustration and misunderstanding during team efforts
What’s included?
- There will be numerous opportunities to network with peers, gain insights from manufacturing operations that are different from your own and build essential skills that will inspire you for improved performance
- You will receive a training manual complete with all materials necessary for the course
- Stylish commemorative award and certificate of completion
- Light breakfast and lunch during session days
Who should attend?
Production or process managers/supervisors, front-line leaders/supervisors, operations managers, quality control leaders, shift leaders, small business owners, and others who want to increase their knowledge of manufacturing methodologies and advance in their profession.
Instructor:
David Athon, President, Athon Group of GA, LLC, has spent most of his career introducing Lean Enterprise principles into manufacturing and transactional environments. He has developed a unique method of integrating Six Sigma and Lean into a single, balanced system. As a certified instructor in both Six Sigma and Lean, David has been educating and consulting since 1996, starting with Lean Enterprise and Continuous Improvement methodologies, adding Six Sigma to his abilities in 2000. As a Master Black Belt, David has held positions in a variety of industries including apparel, metal office furniture, sheet metal, aerospace and commercial air refrigeration.