Celebrating National Manufacturing Day: Strengthening Central PA’s Manufacturing Sector with IMC
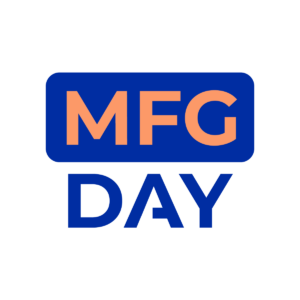
On October 4th, we celebrate National Manufacturing Day, a day dedicated to recognizing the critical role manufacturing plays in the U.S. economy. Here in Central Pennsylvania, manufacturing is a vital industry that fuels local economies, providing high-paying jobs and fostering innovation.
According to recent statistics, manufacturing in Central PA accounts for 14% of the region’s total employment and generates more than $8 billion in annual economic output. The industry supports family sustaining jobs and drives economic growth in communities large and small. With a strong base in advanced manufacturing, food production, metal fabrication, and more – the region is a cornerstone of Pennsylvania’s industrial strength.
At Innovative Manufacturers’ Center (IMC), we are proud to be part of this manufacturing community. As your trusted partner, IMC provides a suite of services that help manufacturers throughout Central PA enhance their processes, boost productivity, train their workforce, and drive innovation. Our goal is to help manufacturers achieve operational excellence, remain competitive, and thrive in an ever-evolving market.
IMC’s Key Services for Central PA Manufacturers:
- Process Improvement: Manufacturers across Central PA face constant pressure to improve efficiency and reduce waste. IMC’s process improvement services are designed to streamline operations, eliminate inefficiencies, and lower costs. Whether it’s reducing lead times or enhancing product quality, we help businesses implement sustainable solutions that boost performance.
- Productivity Enhancement: With the manufacturing sector contributing billions to the economy, maximizing productivity is essential. IMC works with companies to fine-tune their production systems, optimize resource allocation, and improve overall output. Our proven strategies help businesses in Central PA stay ahead of the competition by achieving more with fewer resources.
- Training: Central PA’s manufacturing sector employs a skilled workforce, but as new technologies emerge, ongoing training is crucial. IMC offers comprehensive events and training programs that equip employees with the skills needed to operate new machinery, adopt advanced manufacturing techniques, and improve safety and leadership. By investing in workforce development, we ensure that the region’s manufacturers have the talent they need to succeed.
- Innovation Support: Innovation drives the future of manufacturing, and IMC is committed to helping manufacturers in Central PA by providing expert guidance on incorporating new technologies, from automation to digital manufacturing solutions, and help businesses bring innovative products and processes to life. Our innovation services ensure that Central PA manufacturers are well-positioned to lead in their respective industries.
- People: A skilled, motivated, and cohesive workforce is critical to the success of any manufacturing operation. Your employees drive productivity, innovation, and quality, and their skills and dedication are essential to the long-term success and growth of your business. IMC supports Central PA manufacturers by offering comprehensive services focused on employee engagement, leadership development, change management, and human resources support, essential for the long-term success and growth of Central PA manufacturing.
Celebrating Manufacturing’s Impact in Central PA
Manufacturing in Central PA is more than just an industry—it’s the backbone of our local economy. National Manufacturing Day serves as an opportunity to highlight the impact this sector has on our region’s prosperity and to inspire the next generation to consider careers in manufacturing.
At IMC, we are dedicated to supporting the growth and success of manufacturers in Central PA. Our tailored services help manufacturers improve their efficiency, increase productivity, and innovate for the future. As we celebrate National Manufacturing Day, we remain committed to empowering the manufacturing community and driving economic growth throughout the region.
For more information on how IMC can help your manufacturing business thrive, visit IMCPA.com.
Let’s celebrate the continued success of manufacturing in Central PA this National Manufacturing Day!
Innovative Manufacturers’ Center (IMC) is a trusted service provider for Central Pennsylvania manufacturers, offering tailored solutions to enhance productivity, drive innovation, and improve workforce skills. IMC is committed to helping manufacturers succeed in today’s competitive market.
For more information on National Manufacturing Day, visit MfgDay.com.