In our last article, we talked about step 1 in developing an effective training system. And how critical training has become, as products become, more customized and specialized causing jobs and tasks to become more complex and to continually change. Without effective training, unwanted variation, inconsistency, errors, reduced throughputs and other wastes are inevitable.
Job Breakdown Sheets
As a first step, we described the development of “Job Breakdown Sheets”. A standardized format that describes the ONE BEST WAY to perform a job, listing the steps of the job, how each step is done and why it’s important. Sample Job Breakdown Sheet
How to Train – Job Instruction
Now let’s talk about another consideration. That is, how the training itself is performed. Below is a copy of the “job instruction card” that was part of the Training Within Industry (TWI) training system that was used extensively during WWII. And famously adopted and applied by Toyota as the foundation of the game-changing “Toyota Way”. As you’ll see, the card instructs the trainer on how to plan and prepare to train. And then provides a series of steps for training and ensuring capability and qualification.
It needs to be considered that many of today’s manufacturing jobs are significantly more varied, complex and fast-changing than they were when this methodology was initially developed and implemented. But those basic elements of preparation and instruction can be applied in almost all cases. Consistent and effective instruction methods are critical to an effective training system.
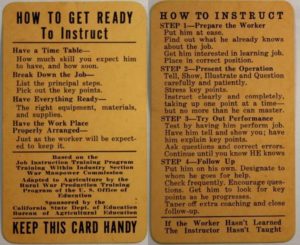
Training System Assessment
Lastly, let’s also mention another important and helpful “tool” for developing an effective training system – a “training system self-assessment”. IMC has developed an assessment that any company can easily and quickly complete to get a solid understanding of the current state of the company’s training system. The tool assesses 5 areas as follows.
- Training roles and responsibilities
- Knowledge and skills of trainers
- Processes / protocols that support the training system
- Training tools and methods
- Training expectations and metrics
In our next article we’ll take a closer look at the Training System Self-Assessment. Meanwhile, if you’d like a copy of the assessment, email me at russl@imcpa.com.